What is Forward & Backward Scheduling? (And How it Relates to Logistics)
Forward and backward scheduling refers to the order in which you complete deliveries based on customers timing preferences.
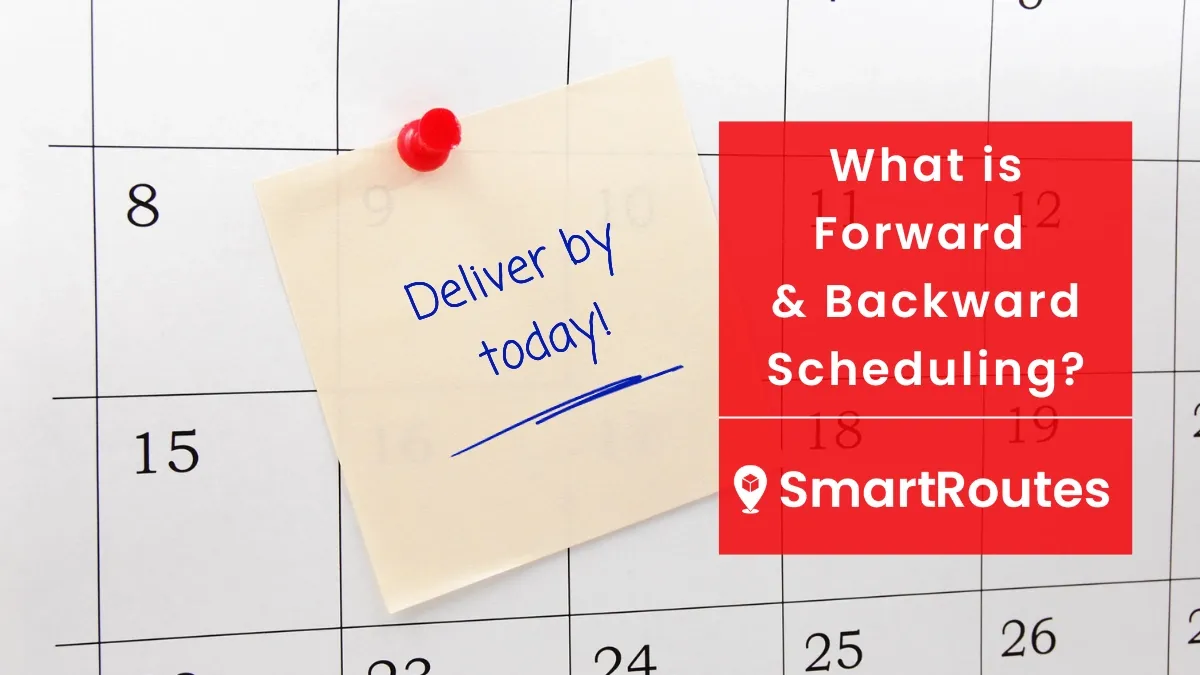
Regular readers of our blog will be no strangers to the increasing demands of customers facing the last-mile delivery industry. Working with both retailers and third-party logistics businesses to solve their delivery problems, they are constantly reminding us just how much is expected of them in the age of convenience.
To meet these demands, businesses have turned to tried-and-tested logistics strategies that can deliver on promises to customers, while making their operations more efficient. One of these strategies is forward and backward scheduling.
We’ll take a look at what forward it involves, define it and get into the thick of how it works for the delivery and logistics industry. We’ll also use some practical examples of how we have helped delivery businesses establish their own backward and forward scheduling processes with the help of route planning technology.
So whether you're a courier, retailer, or just looking to learn some more about the topic, we think you’ll find what you’re after.
Why are businesses using backward and forward scheduling?
What scheduling strategy should a delivery business use?
How Delivery Management Software takes the thinking out of delivery scheduling
Schedule deliveries with ease using SmartRoutes
What is Forward Scheduling?
Forward scheduling is a method of planning the desired completion date of a specific task. With forward scheduling, the idea is that you start and complete the job at the earliest date possible.
For example, if a restaurant has recently renovated its kitchen and ordered new appliances, it may plan to install all of the new appliances from Monday to Friday in one week. If you are the one delivering the new cooker, you would schedule the delivery for Monday morning under the principle of forward scheduling.
As the name suggests, you are planning ‘forward’ your deliveries for that week with additional orders to follow.
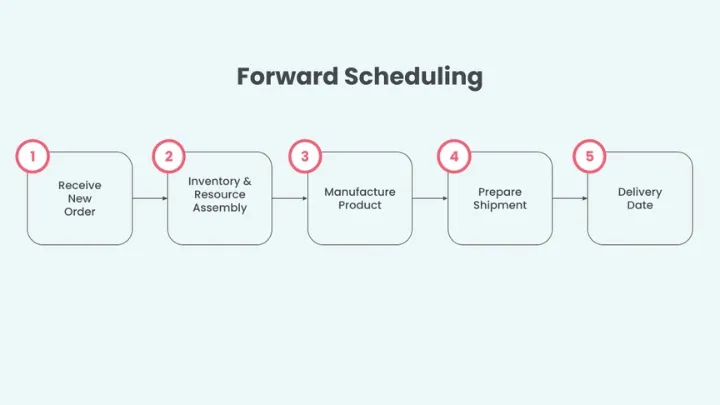
What is Backward Scheduling?
Backward scheduling is the opposite of forward scheduling and is a method of planning the desired completion date of a task at the latest date possible.
Using our example of a restaurant installing all of their new appliances in a renovated kitchen in one week from Monday to Friday, the idea is that you would schedule the delivery of the cooker for last thing Friday.
As the name suggests, you are planning your deliveries ‘backward’ from the Friday of that week, with additional orders from customers being added to your schedule in reverse order on your calendar.
In simple terms, the difference between backward and forward scheduling is simply the order in which you fill your schedule either working forward from the earliest time and date possible, or the latest time and date respectively.
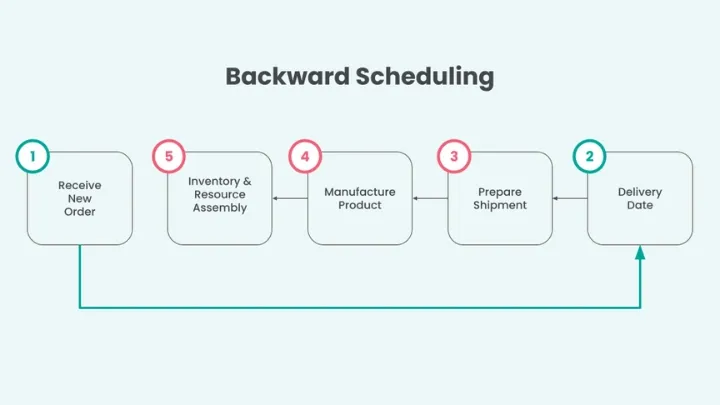
Why are Businesses using Backward and Forward Scheduling?
While many logistics businesses opt for some variation of backward and forward scheduling as part of their operations, deciding on which one often depends on a variety of factors including:
- The type of delivery business they operate (last mile, long-haul, international shipping, etc.)
- The type of goods or services they deliver (perishable vs. non-perishable, missions-critical vs. non-mission-critical, etc.)
- Level of urgency and demand on the customer end
- Service Level Agreements with end customers (some customers will have stronger contracts than others)
While these factors play a large part in your decision, it may also come down to personal preference or even gut feeling on what you think is right for your business. For many niche delivery businesses, they will find that there is a greater degree of variance in terms of demands, urgency, and preferences among their customers.
SmartRoutes Route Planning Software
Streamline your entire delivery process, all from one platform
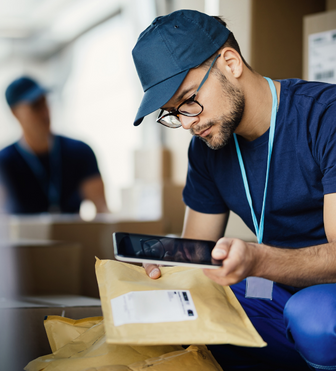
How Brady Family use forward scheduling for their holiday season delivery service
If we take the example of a business that delivers its own farm-raised turkeys and hams directly to customers in advance of Thanksgiving and the holiday season, forward scheduling may be the best option.
This was the case when Bradys Family Ham offered an online ordering system for those who wanted to be fully prepared for the year's most important meal. The truth is, a lot of us tend to leave our holiday shopping to the final weeks (or in my case, days!) of the holiday season.
However, many simply love being prepared for their favorite day of the year and getting their shopping done early.
By utilizing forward scheduling, they were able to schedule their orders from the beginning of the week (Monday morning) in the hope that all orders would be complete before the end of the working week (Friday evening). The benefit of this was twofold:
- Drivers that finished routes earlier in the week could lend a hand in preparing orders for the following week
- It gave a better foresight to the delivery planners as the weeks progressed and they got a better sense of how busy they expected the following week to be.
In this case, forward scheduling was the best option for a food delivery logistics operation that was new, seasonal, and relatively unpredictable in terms of how many orders to forecast.
How B. Grennan Transport uses backward scheduling to cater to tricky agri-supplies deliveries
There can be little doubt that farmers are amongst the hardest-working people in our societies. Whether they work with animals or tillage, the work they do is labor-intensive and time-critical. When your crops and animals rely on you to feed and water them daily, staying on top of the endless number of other tasks can be a struggle.
For our client, B. Grennan Transport, this also poses a challenge. They deliver agri supplies such as animal feed and fertilizer to farms across the entire country of Ireland. When returning goods, they are usually dropped off in large yards or grain silos that have plenty of capacity. For other farmers, they will have less predictability in terms of forecasting the amounts of feed or grain they will need, and when they tend to run out.
In this case, backward scheduling works best for Grennans; it allows them to plan their deliveries to regular/routine customers later in the week, leaving more time and flexibility to serve ad-hoc customers who suddenly find themselves without feed for their animals. Accommodating flexibility, unexpected changes, and urgent requests to schedules can make backward scheduling a valuable strategy for logistics firms and businesses.
In fact, with SmartRoutes Agri Delivery Software, the interactive customer mapping dashboard alerts Grennans when a farmer should be due an order based on past activities. As they schedule deliveries backward, this can allow them to proactively reach out to customers that a truck will be in the area. This has the benefit of maximizing available capacity on trucks and cutting down on unnecessary mileage.
What Scheduling Strategy should a Delivery Business Use?
Forward and backward scheduling are two important strategies that last-mile delivery companies can use to optimize their operations and improve customer satisfaction. These scheduling methods offer distinct benefits:
Forward Scheduling
1. Meeting Customer Expectations:
Forward scheduling helps ensure that deliveries are made within the promised time windows, which is crucial for meeting customer expectations and enhancing customer satisfaction.
2. Optimized Routing
It allows the company to plan routes efficiently by considering factors such as traffic conditions, delivery windows, and driver availability. This can reduce delivery times and operational costs.
3. Real-Time Adjustments
Forward scheduling can accommodate real-time changes, such as delays or route modifications, by adjusting schedules accordingly. This flexibility is vital for adapting to unforeseen circumstances.
4. Improved Resource Allocation
It helps allocate resources effectively, including drivers, vehicles, and delivery personnel, to meet demand while minimizing idle time and operational costs.
5. Enhanced Inventory Management
Forward scheduling can integrate with inventory management systems, ensuring that the right products are available for delivery at the right time, reducing stockouts and excess inventory costs.
Backward Scheduling
1. Deadline Focus
Backward scheduling starts with the desired delivery deadline and works backward to determine when the order needs to leave the distribution center or warehouse. This is especially useful for time-sensitive deliveries.
2. Minimized Overtime Costs
By calculating the optimal departure times for deliveries, backward scheduling can help minimize overtime costs for drivers and ensure that work hours are efficiently utilized.
3. Increased On-Time Deliveries
By ensuring that deliveries are planned to arrive just in time for their scheduled appointments, backward scheduling can improve the on-time delivery performance, reducing customer complaints.
4. Resource Optimization
Like forward scheduling, backward scheduling can optimize resource allocation, ensuring that the right vehicles and personnel are available to meet delivery deadlines.
5. Compliance with Service-Level Agreements (SLAs)
Backward scheduling helps companies adhere to SLAs and contractual obligations by ensuring that deliveries are made within the specified timeframes.
Forward & Backward Hybrid Scheduling Benefits
- By combining forward and backward scheduling, last-mile delivery companies can strike a balance between meeting customer expectations (forward scheduling) and efficiently utilizing resources to meet delivery deadlines (backward scheduling).
- These scheduling methods can help reduce operational costs, improve delivery accuracy, and enhance overall customer satisfaction.
- Integration with advanced technology and real-time tracking can further enhance the benefits of both scheduling methods by allowing for dynamic adjustments based on changing conditions.
In summary, forward and backward scheduling are valuable tools for last-mile delivery companies, offering benefits related to customer satisfaction, resource optimization, cost reduction, and adherence to delivery deadlines. The choice between the two methods or a combination of both depends on the specific needs and priorities of the company and its customers.
How Delivery Management Software Takes the Thinking out of Delivery Scheduling
Delivery Management Software is designed to help businesses schedule deliveries in the way that works best for their operations.
SmartRoutes is just one solution available to businesses but it does offer unrivaled customization for specific business needs based on their individual route scheduling needs.
To understand the role it plays, we’ve broken it into a few key areas it improves:
Route Optimization
At the core of most delivery management solutions is a feature that has transformed the multi-stop delivery industry: route optimization.
Route Optimization uses computational power to calculate the quickest routes based on various factors such as traffic conditions, delivery windows, vehicle capacities, and more.
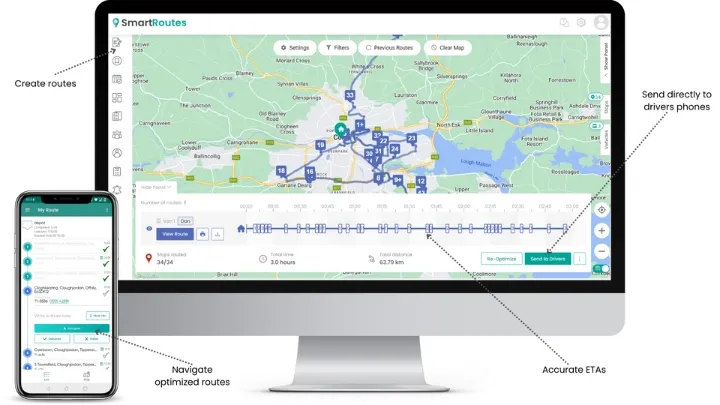
Live Route Adjustment
By incorporating live tracking, delivery management solutions allow businesses to make alterations to delivery routes on the fly.
For example, if a new collection comes in from a customer during a route, it can be automatically added to the route at the most convenient point, without any human data input.
This can make backward scheduling much more achievable.
Delivery Notifications
Automating the communications to customers regarding their estimated delivery times, and including tracking links, allows customers to communicate any changes in their schedules and make better plans to make delivery possible.
Order Management Integration
By integrating with order management systems, delivery management solutions can ass orders to delivery routes at a moment's notice without any human input.
An order canceled while the driver is en route?
Again, that can be recorded on and the stock quantity updated on the order management system automatically.
Driver Management
No matter which scheduling strategy you choose for your business, managing drivers' rosters can be a nightmare. Availability, driver regulations, and vehicle capacities can create a logistical nightmare when trying to allocate orders to routes.
Fortunately, delivery management solutions allow you to simply record all of this and then create routes based on the parameters you’ve chosen.
With route scheduling being one of the most time-consuming parts of a logistics planner's job, this makes life much easier.
Schedule Deliveries with Ease Using SmartRoutes
At SmartRoutes, we’ve helped hundreds of clients from the logistics and retail determine the best scheduling strategy and process for their own unique business needs.
While it can seem like a daunting task to establish a strategy that will work, having the experience of professionals who dedicate their time to studying delivery processes and workflows can bring much greater clarity and understanding to the planning process.
In studying the delivery processes of thousands of logistics businesses around the world, we created a delivery management solution that is flexible and customizable for even the most complicated of scheduling strategies.
If you’re struggling with a decision on what scheduling approach would work best for your business, try out SmartRoutes for free to see how we can help!
Frequently asked questions
1. Is forward and backward scheduling suitable for all types of businesses?
Forward and backward scheduling are adaptable strategies that can be employed by a wide range of businesses, but their suitability depends on specific operational needs and industry requirements. Industries with strict delivery deadlines or perishable goods may find backward scheduling more suitable, while forward scheduling could be advantageous for businesses focused on customer convenience and prompt service.
2. Can businesses combine both forward and backward scheduling?
Yes, businesses can certainly combine elements of both forward and backward scheduling to create a hybrid scheduling approach. This approach allows companies to strike a balance between meeting customer expectations (forward scheduling) and efficiently utilizing resources to meet delivery deadlines (backward scheduling). The combination of these strategies can be customized to suit the unique needs of a business.
3. What challenges can arise when implementing forward or backward scheduling?
Implementing forward or backward scheduling can present several challenges, including adapting to changing customer demands, managing unforeseen delays or disruptions, and fine-tuning schedules based on real-time data. Additionally, coordinating and optimizing routes, managing driver availability, and ensuring compliance with delivery windows can be complex tasks when implementing these scheduling methods.
4. Why is backward scheduling more common than forward scheduling?
Backward scheduling is often more common in industries like logistics because it focuses on meeting specific delivery deadlines. This approach is particularly beneficial for time-sensitive deliveries and helps minimize overtime costs. However, the choice between backward and forward scheduling ultimately depends on the nature of the business, customer demands, and industry-specific requirements.
5. How do you calculate backward scheduling?
Calculating backward scheduling involves starting with the desired delivery deadline and working backward to determine when the task or delivery needs to commence. To calculate backward scheduling, you'll need to consider factors such as the delivery deadline, travel time, processing time, and any other relevant time constraints. This method ensures that the task or delivery is completed just in time to meet the specified deadline.
If you enjoyed this blog, you might also be interested in:
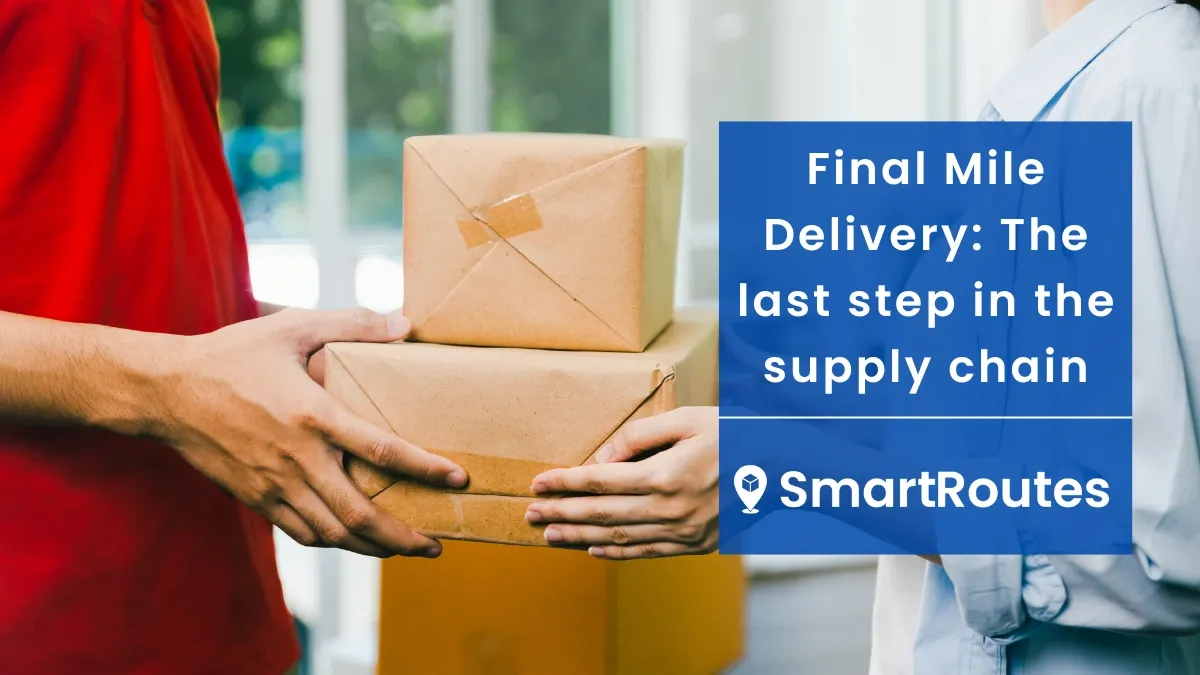
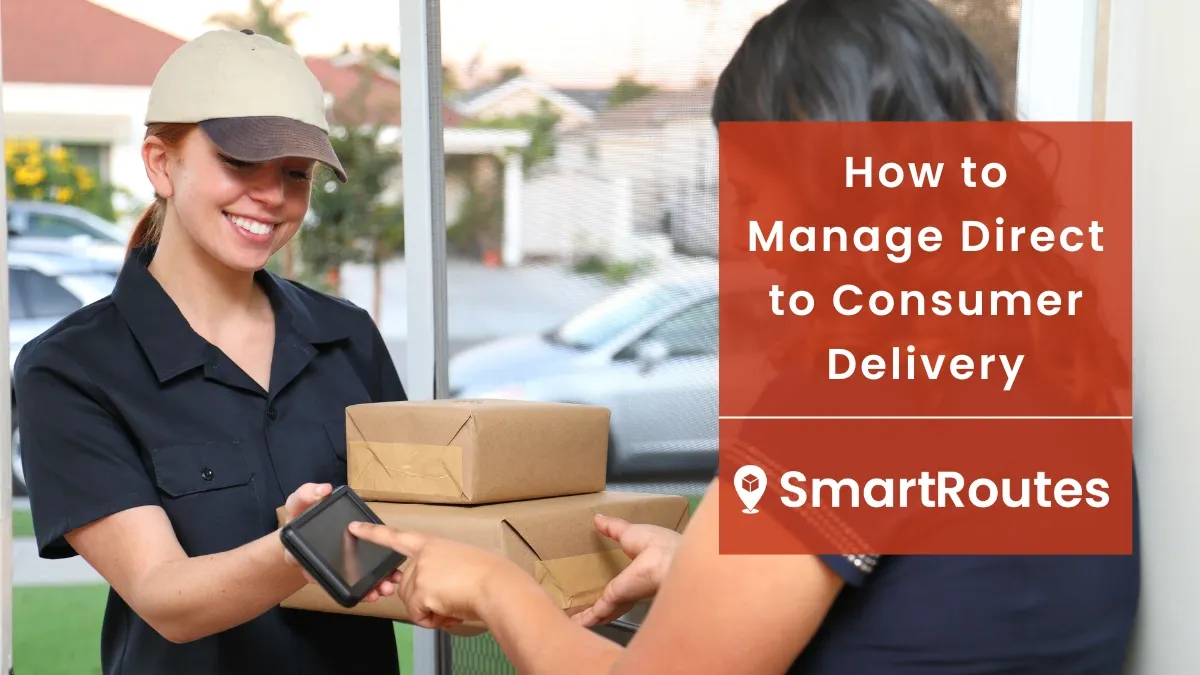