Maximizing Delivery Accuracy: A Guide
In this blog, we will take a closer look at delivery accuracy, how it can be measured, the causes of inaccurate deliveries and our recommendations for improving delivery accuracy in your business.
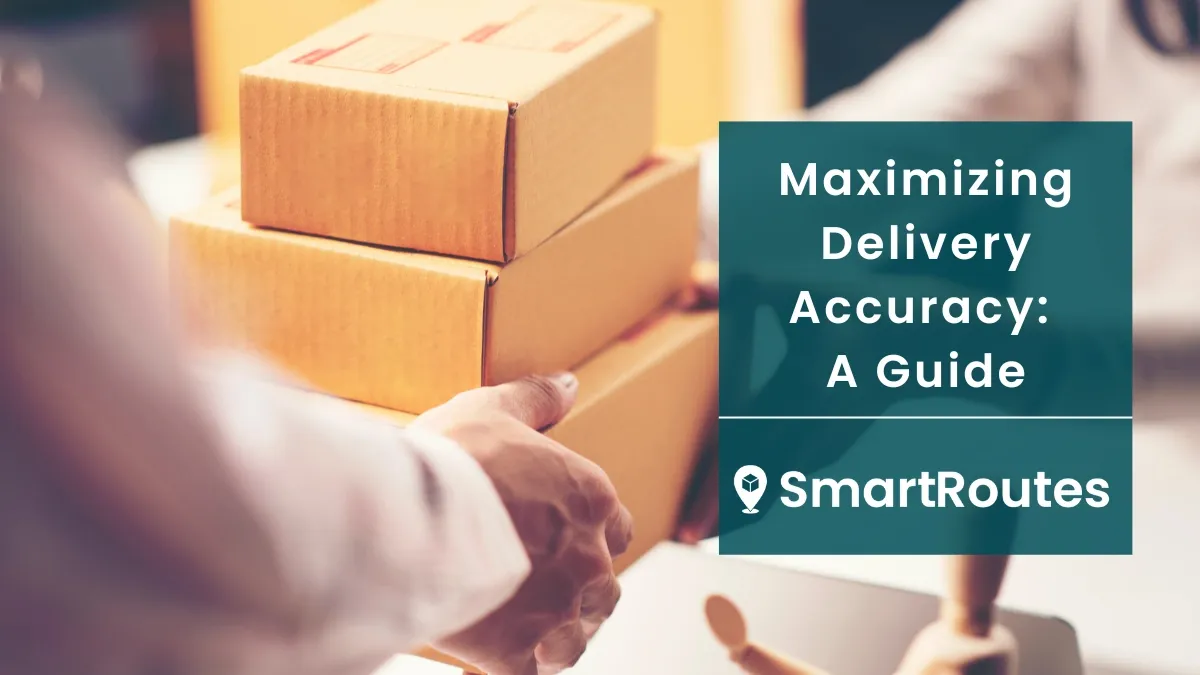
The true measure of success for any logistics or delivery team lies in the seamless orchestration of deliveries. Deliveries are expected to be timely, precise and reliable. Customers often base their entire judgement of a company's online ordering process entirely on the handover of the order. While this may appear unfair to businesses that have spent time and money on getting the entire delivery process right, only to fall short at the last mile, it is the most memorable interaction the consumer has with your company.
It may be common sense that parcels should arrive at the designated doorstep, that fragile items are handled with care, and that time-sensitive goods maintain their freshness throughout the journey, however - things like human error and unforeseen circumstances can hinder the desired outcome.
Every successful delivery not only fulfills an order but also nurtures trust between businesses and their clientele. It sets the stage for both repeat business and positive word-of-mouth.
In this blog, we will take a closer look at delivery accuracy and how it affects the delivery experience, how it can be measured, the causes of inaccurate deliveries and our recommendations for improving delivery accuracy in your business.
How do you Measure Delivery Accuracy?
The Causes of Inaccurate Deliveries
What is the Outcome of Poor Delivery Accuracy?
How to Improve Delivery Accuracy
What is Delivery Accuracy?
Delivery accuracy measures the success of your delivery process, from the order being placed, to picking and packing in the warehouse, to transit and final delivery, without errors or delays. This metric is arguably one of the most important to measure in your delivery process. It serves as a testament to the efficiency and reliability of a business's logistical operations.
Delivery accuracy isn't solely about meeting basic expectations for the delivery experience, but surpassing them with a commitment to precision, attention to detail, and a relentless pursuit of customer satisfaction.
Improve Delivery Accuracy with SmartRoutes
Streamline your entire delivery process, all from one platform
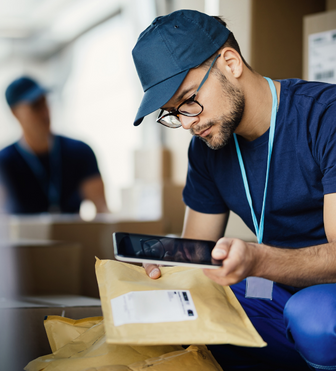
How do you Measure Delivery Accuracy?
Measuring delivery accuracy involves a thorough examination of the entire delivery journey, starting from the moment an order is received to the delivery at the customer's doorstep.
You can calculate your delivery accuracy as follows:
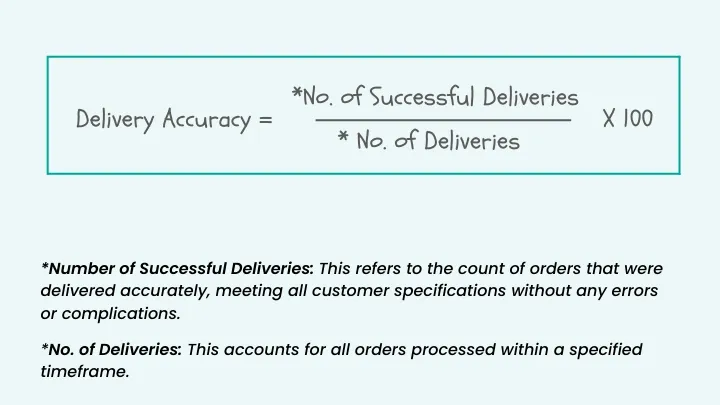
Once you have your score, whether you need to make improvements or maintain your high standard, you should check the following:
- Ensure each item is the correct size, colour, and meets every specification outlined in the order.
- Identify any discrepancies or mishaps that might occur along the way eg. incorrect items or an unexpected delay, addressing these issues promptly helps maintain the integrity of your delivery accuracy.
- Verify successful deliveries against their intended destinations to confirm that each package has reached its rightful recipient without any errors or unexpected detours.
The Causes of Inaccurate Deliveries
The earlier you catch inaccuracies in the delivery process, the better! Errors in deliveries often occur due to:
- Human Errors: One of the primary culprits behind inaccurate deliveries is human error. From mishandling inventory in the warehouse to inaccuracies during the crucial order-picking stage, these errors can introduce discrepancies in the delivery process.
- Reliance on Manual Processes: Relying solely on manual processes can magnify the risk of inaccuracies. Manual interventions at various stages of the delivery journey, without the aid of automated systems or checks, increase the potential for errors to infiltrate the process.
- Poor Route Planning: Inadequate planning of delivery routes can trigger a domino effect of issues. It can result in delayed deliveries or, in more severe scenarios, the misdirection of parcels to incorrect addresses. This deficiency in route planning amplifies the likelihood of deviations from optimal paths, disrupting the smooth flow of deliveries.
- Insufficient Communication: Inaccuracies often arise from breakdowns in communication between different stages of the delivery process. Lapses in communication between warehouse staff, delivery personnel, and customer service teams can lead to misunderstandings, resulting in incorrect order fulfillment or delays.
- Inadequate Inventory Management: Inaccurate deliveries can stem from inadequacies in managing inventory. Issues such as incorrect stock counts, misplaced items, or discrepancies between actual inventory and recorded data can lead to errors during order fulfillment and subsequent deliveries.
- Appropriate Safeguards Not in Place: Inaccuracies can occur when necessary precautions are lacking, especially during contactless deliveries. Instances like inadequate measures to protect against porch pirates might result in parcels being stolen or lost, impacting the accuracy of deliveries.
- Customers Not Kept in the Loop: Inaccuracies can arise due to a lack of communication with customers. If customers are not informed about their delivery schedules or tracking information, they might not be present to accept their orders. This can lead to anxiety and dissatisfaction, impacting the overall accuracy of the delivery process.
- Items Not Assigned to Correct Vehicle: Inaccuracies might result from items being allocated to incorrect vehicles during loading. For instance, perishable or refrigerated orders mistakenly loaded into non-refrigerated vehicles could compromise the integrity of goods and lead to inaccurate deliveries.
- Poor Delivery Scheduling: Inaccurate deliveries may occur due to suboptimal planning in delivery route scheduling. Overestimating or underestimating delivery times due to inadequate planning can significantly affect on-time delivery rates, leading to discrepancies in meeting customer expectations.
Identifying these causes sheds light on the vulnerabilities within the delivery process, emphasizing the need for proactive measures to mitigate these challenges and improve the accuracy of deliveries.
What is the Outcome of Poor Delivery Accuracy?
Increased Operational Costs: Failed, missed, or re-deliveries add a substantial financial strain on businesses. These inaccuracies translate into increased fuel expenses and driver costs. Each failed delivery not only consumes additional resources but also depreciates operational efficiency, burdening the company with avoidable expenditures.
Costly Returns: Inaccurate orders result in the need for customers to return their orders. Retrieving incorrect items demands additional logistics efforts, including collection or covering the cost of returns. Simultaneously, re-delivery or refunds of the original order, alongside the re-selling of the incorrectly delivered products, increases expenses further.
Decreased Customer Retention: Poor delivery accuracy can significantly decrease customer retention. Customers will switch to alternatives if they encounter unreliable deliveries. This can also lead to potential negative word-of-mouth.
Risk of Chargebacks: Inaccurate deliveries increase the likelihood of customers disputing charges with their banks. Chargebacks not only result in immediate revenue loss but also dent the company's credibility. Furthermore, excessive chargebacks may incur penalties and tarnish the company's financial standing.
Disrupted Supply Chain Flow: Poor delivery accuracy disrupts the overall flow of the supply chain. Inaccuracies in deliveries can lead to delays in subsequent processes, impacting inventory management, production schedules, and distribution timelines. These disruptions may cascade down the supply chain, affecting multiple aspects of operations.
How to Improve Delivery Accuracy
Identify and Address Issues
Identifying and addressing issues within your delivery process is crucial for ensuring efficiency and customer satisfaction:
- Current Process Analysis: Begin by assessing your existing delivery methods. Look at key metrics like delivery times, success rates, and customer feedback. Identify bottlenecks or inefficiencies that might be hindering the smooth flow of deliveries.
- Feedback Collection: Gather feedback from various stakeholders involved in the delivery chain - customers, delivery personnel, warehouse staff, and customer service representatives. Understanding their perspectives can uncover issues that might not be immediately apparent.
- Technology and Tools Evaluation: Assess the technology and tools used in the delivery process. Are there any outdated systems causing delays or errors? Look for modern solutions that could streamline operations, such as route optimization software or inventory management systems.
- Forecasting Future Challenges: Anticipate potential issues that could arise based on changes in demand, seasonal variations, or market trends. This proactive approach helps in preparing strategies to tackle those challenges beforehand.
By diligently examining your current delivery process, anticipating future challenges, and implementing strategies to address these issues, you can optimize your delivery operations for enhanced efficiency and customer satisfaction.
Implement Technology in the Warehouse
Implementing technology in the warehouse can significantly enhance inventory management and overall efficiency:
- Inventory Tracking Systems: Introduce a robust inventory tracking system that utilizes barcodes or RFID tags. These systems provide real-time updates on inventory levels, locations, and movement within the warehouse. They streamline stock counting processes and minimize errors associated with manual tracking.
- Warehouse Management Software (WMS): Invest in a WMS tailored to your warehouse operations. They improve order accuracy, reduce picking times, and enhance overall warehouse productivity.
- Predictive Analytics: Implement predictive analytics tools that analyze historical data to forecast inventory demands accurately. This helps in proactive capacity planning, preventing stockouts or overstock situations.
- Integration with Supply Chain: Integrate your warehouse technology with the broader supply chain management system. This facilitates seamless data flow between suppliers, distributors, and the warehouse, ensuring a synchronized and efficient supply chain process.
Establish a Verification Procedure
Establishing a verification procedure for picking is crucial for maintaining accuracy and quality control:
- Weight Verification: Implement a weight verification process where picked items are cross-checked against their expected weights. Use scales or automated systems to ensure that the weight matches the predetermined standard. Any discrepancies trigger an immediate investigation or rechecking process.
- Tag Auditing: Utilize tag auditing as a verification method. Each item picked is checked against its corresponding tag or barcode. This involves scanning or manually checking tags to confirm that the correct product has been picked. Any mismatches or errors are flagged for correction before further processing.
- Barcode/RFID Scanning: Introduce barcode or RFID scanning as part of the verification process. Every item picked is scanned to ensure alignment between the item code scanned and the one expected for that specific order. This method ensures precise identification and minimizes errors caused by similar-looking products or packaging.
- Random Sampling Checks: Conduct random sampling checks at different stages of the picking process. This ensures that accuracy is maintained consistently throughout the workflow. Random checks discourage errors and maintain a high level of accuracy among the picking staff.
By implementing a robust verification procedure in the picking process, you ensure accuracy, reduce errors, and maintain high standards of quality control, ultimately enhancing customer satisfaction and loyalty.
Optimize Vehicle Loading
Optimizing vehicle loading is essential for maximizing efficiency and ensuring safe transportation of goods:
- Categorize Goods and Orders: Classify goods based on their nature, fragility, size, and temperature requirements. Group orders that share similar delivery specifications, ensuring compatibility with the type of vehicle required for transportation.
- Loading Plan Creation: Develop a loading plan that aligns with vehicle specifications and optimizes available space. Designate specific zones within the vehicle for different types of goods, segregating fragile items, perishables, and bulkier goods to prevent damage or spoilage during transit.
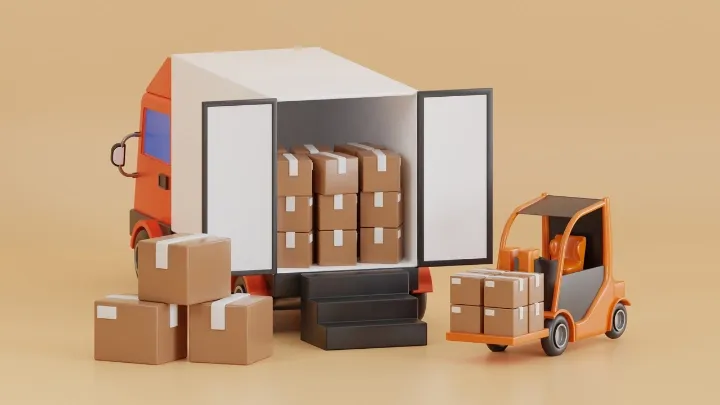
- Software-Assisted Optimization: Implement specialized software or tools designed for load optimization. These programs analyze the dimensions, weight, and characteristics of each item and suggest the most efficient way to load goods into vehicles to maximize space utilization while maintaining safety regulations.
- Route and Delivery Schedule Consideration: Factor in the delivery routes and schedules while loading vehicles. Ensure that items needed for early deliveries are loaded last for easy access, minimizing unnecessary handling and rearrangement of goods during stops.
By employing these strategies, you can optimize vehicle loading based on specific vehicle specifications, utilize software for efficient space management, and ensure that goods are transported safely and effectively to their destinations. This approach leads to cost savings, reduced transit times, and improved customer satisfaction through timely and intact deliveries.
Implement Scheduling Software
Adopt specialized delivery scheduling software that streamlines the entire delivery process:
- Enhanced On-Time Performance: Utilize the software's route optimization capabilities to plan efficient delivery routes, minimizing travel time and optimizing the allocation of deliveries among drivers. This helps in improving on-time delivery rates and meeting customer expectations for prompt service.
- Customer Communication and Notifications: Leverage scheduling software to keep customers informed throughout the delivery journey. Automated notifications via SMS or email update customers about their delivery status, estimated time of arrival, and any delays, enhancing transparency and managing expectations.
- Customizable Delivery Notes: Utilizing scheduling software equipped with a delivery driver app allows for seamless access to customer-provided delivery instructions during the delivery process. These instructions, ranging from leaving packages in specified locations to sharing access codes, ensure tailored and convenient delivery experiences for customers.
- Real-Time Updates and Tracking: Enable real-time tracking functionalities in delivery apps, allowing customers to track the location of their package and monitor its progress. This transparency builds trust and reduces inquiries about delivery status, leading to a smoother customer experience.
Implementing scheduling software not only streamlines the delivery process but also empowers customers with control over their deliveries, resulting in improved satisfaction, increased efficiency, and higher on-time delivery rates.
Offer Delivery Windows
Providing delivery windows offers customers flexibility, increasing the likelihood of them being available to receive their orders:
- Offering Flexible Delivery Windows: Providing customers with a range of delivery time windows caters to their schedules and commitments. This flexibility allows customers to select a time that suits them best, minimizing the chances of missed deliveries and enhancing convenience.
- Customer Convenience and Satisfaction: By accommodating various delivery windows, customers feel empowered and valued. It reduces frustration related to waiting for deliveries and increases the probability of successful handovers, contributing to an increase in delivery accuracy.
- Impact of Delivery Handover on Brand: Recognize the significance of the actual handover of the parcel to the customer. This moment is crucial as it directly influences the customer's perception of the entire delivery experience. A courteous, friendly, and professional delivery interaction leaves a positive impression. Conversely, a negative experience can deter customers from ordering again and might lead to negative word-of-mouth.
By emphasizing the importance of providing flexible delivery windows and recognizing the impact of the handover experience, businesses can significantly enhance customer satisfaction, foster loyalty, and increase the likelihood of repeat orders.
Use Route Planning Software
Leveraging route planning software offers several benefits as well as accurate deliveries:
- Efficient Delivery Routing: Route planning software optimizes delivery routes based on various factors like distance, traffic, and delivery priorities. This efficiency minimizes travel time and fuel consumption while ensuring timely deliveries.
- Accurate Location Deliveries: The software utilizes GPS and mapping technologies to pinpoint accurate delivery locations. This precision minimizes errors and ensures that deliveries are made to the correct addresses, reducing instances of misdelivery or rerouting.
- Proof of Delivery (POD): The software allows for the capture of proof of delivery through various means such as digital signatures, photos, or barcode scans. This serves as concrete evidence that the delivery was completed, providing assurance to both the company and the recipient
- Real-time Tracking and Monitoring: The software enables real-time tracking of delivery vehicles. This feature allows managers to monitor the progress of deliveries, foresee potential delays, and proactively address any issues that may arise during the delivery process.
Utilizing route planning software not only ensures accurate deliveries but also enhances operational efficiency, transparency, and customer satisfaction. It serves as a vital tool for improving delivery logistics while providing comprehensive records for accountability and analysis.
Improve Your Delivery Accuracy with SmartRoutes
With SmartRoutes, achieving pinpoint accuracy in delivery logistics becomes effortless. Our advanced algorithms factor in real-time data, delivery constraints, and vehicle capacities to craft the most optimal routes possible.
The result? Streamlined operations, minimized delivery times, and improved overall productivity.
Try SmartRoutes today with our 7 day free trial, you’ll start to see your delivery accuracy go up right away!
Frequently asked questions
1. Why is delivery accuracy crucial for businesses?
Delivery accuracy significantly impacts customer satisfaction, fostering loyalty and repeat business. It minimizes operational costs associated with returns, re-deliveries, and customer service resolutions. Accurate deliveries enhance brand reputation and trust, driving positive word-of-mouth referrals.
2. What steps can businesses take to minimize delivery inaccuracies?
Implement advanced inventory management systems to streamline operations and reduce errors. Introduce verification processes like weight checks and tag audits to ensure order accuracy. Utilize scheduling software for optimized routes and delivery timelines, enhancing on-time deliveries. Offer delivery windows to provide flexibility and manage customer expectations effectively.
3. How can businesses measure their delivery accuracy effectively?
Utilize key performance indicators (KPIs) such as Perfect Order Rate, on-time delivery rates, and order accuracy metrics. Collect and analyze customer feedback, track return rates, and assess discrepancies to gauge accuracy. Leverage data from delivery performance software and systems to quantify accuracy levels.
4. What role does technology play in improving delivery accuracy?
Advanced technologies like route optimization software streamline delivery routes, minimizing delays and errors. Automated inventory systems reduce human error in picking and packing, enhancing order accuracy. Real-time tracking systems and verification tools ensure visibility and accuracy throughout the delivery process.
If you enjoyed this blog, you might also be interested in:
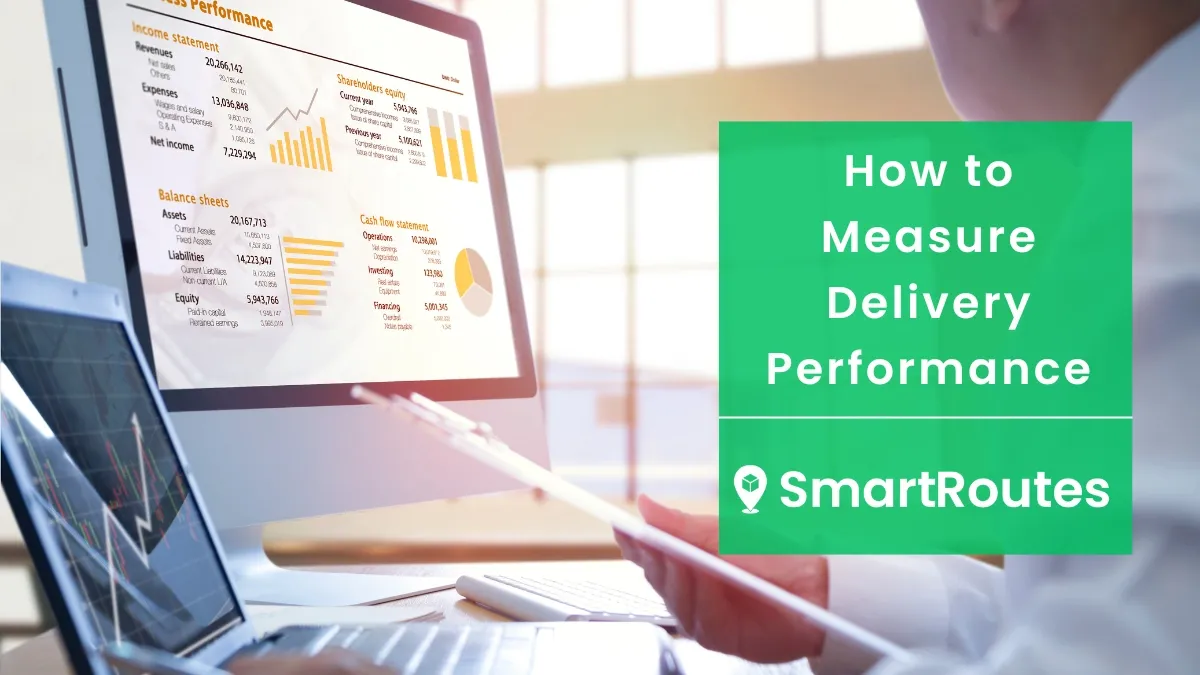
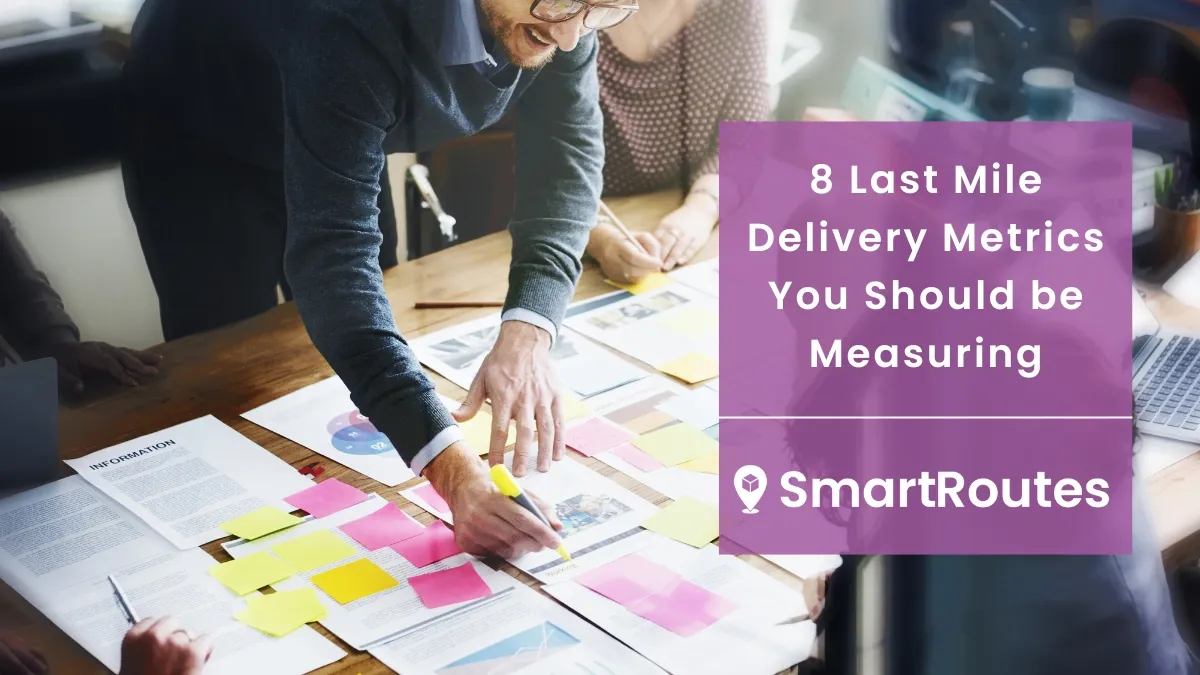